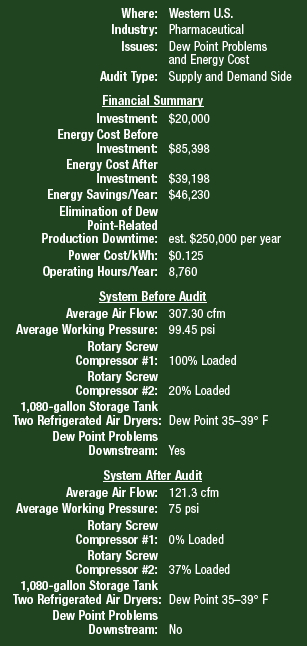
A. Introduction
This West Coast
pharmaceutical facility has a very clean and organized compressed air
system. All equipments is in good working order in the compressor room.
The compressor room itself is very clean and well ventilated. The
management requested a compressed air system audit for two reasons:
- Production problems and downtime resulting from the presence of moisture in the compressed air lines. The compressor room dryers were functioning properly so how could this happen?
- Awareness of the high cost of compressed air and a desire to find ways to reduce compressed air demand.
This article will
describe the actions taken to address these two issues. The facility
operates “24/7” so we have 8,760 operational hours per year. The
average electrical rate at this facility is $0.12 kW/h. The power cost
formula used is based upon the facility’s current operating conditions
of 3.89 CFM/BHP and 95% average motor efficiency.
Power Cost = (BHP *0.746 * 8,760 hours x $0.12 per kW/h) / Avg. Motor Efficiency (95%)
The focus of this audit is on the “Demand
Side” with the very top priority being to identify the root cause of the
presence of moisture in the compressed air lines.
B. Compressor Room Review
The Compressor Room is extremely clean and
well ventilated. There are two rotary screw compressors which are oil
lubricated and air-cooled. The air is dried by two parallel
refrigerated air dryers. The air then goes into a common header and
flows into a 1,040 gallon air storage tank. The air then flows into a
Intermediate Flow Controller. From here the compressed air leaves the
compressor room and enters the facility. The average CFM per BHP
between the two air compressors is 3.80 CFM per BHP.
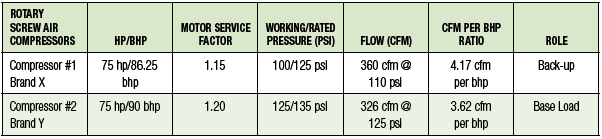
Upon entering the compressor room we noted
an audible air leak in Compressor #2. We found the leak to be coming
from the air end and recommended that the air compressor service
provider be contacted immediately. Both air compressors are operating
via modulation control. Compressor #2 acts as the base load machine
while Compressor #1 is the back-up machine when pressure falls to a
predetermined set point.
The two refrigerated air dryers are in good
working condition and functioning properly. They are designed to
produce a dewpoint range between 33 F and 39 F at a maximum flow of 330
CFM at 100 psi. We took dewpoint measurements at the compressor room
outlet (for one week) and found that the average dewpoint achieved was
36 F. This correct dryer performance is what has the facility
bewildered by the presence of water in the compressed air lines in the
factory. It is worth noting that the dryers are not capable of drying
the full air output capacity of the air compressors if factory demand
should increase. The dryers have integrated 1 micron particulate
filters. We recommend that the facility install a 0.01 ppm oil
coalescing filter to protect against oil contamination downstream.
The 1040 gallon air storage tank is
adequate for the air demand in the facility. During production we
recorded an average air flow of 307.30 CFM which means the tank is
providing 3.38 gallons of storage per 1 CFM of air storage. The tank is
also piped properly (after the air dryer) with air entering the bottom
of the tank and exiting the top – providing more surface area for
moisture to be separated and fall to the bottom of the tank.
C. Solving the Problems with Moisture
It was initially reported that the plant
was “having problems resulting from an excess of water in the compressed
airlines”, with the primary area of concern being the small cylinders
in the plant. As a standard part of our audit procedure we took dewpoint
readings. These test showed a refrigerated drying system according to
its specifications. The data depicted below shows a very steady
dewpoint with less than half a degree fluctuation over a ten minute time
span. The 36 °F average dewpoint is well within the expected range of
performance for these dryers.
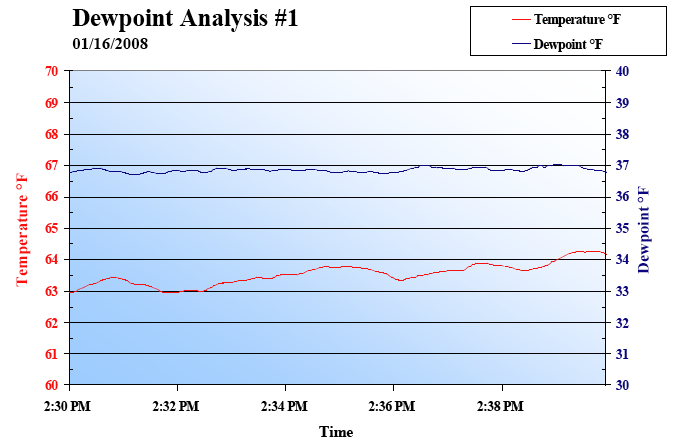
As a result of the ongoing condensation
issues, the factory had taken some actions in hopes of remediating the
problem. The solution the plant put into place was to install water
separators on each line and open the drains on
Filter-Regulator-Lubricators (FRL’s) throughout the plant. We found a
total of 18 FRL units with the drains open, exhausting approximately 2
CFM each worth of compressed air, totaling 36 CFM worth
of compressed air. The problem with this is that the only thing
exhausting through the drains was compressed air, thereby decreasing
plant pressure at the same time.
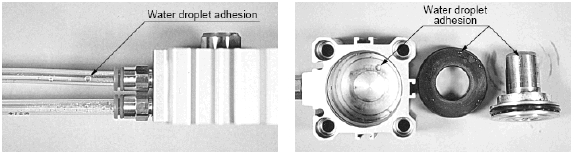
Moisture in Pneumatic Cylinders Created Production Down-Time
Adiabatic Expansion
Through further invest
igation
we found the root of the problem. When air is discharged from the
piping between the cylinder and the valve, the temperature of the air
drops due to adiabatic expansion. . If the atmospheric dewpoint of
the supply air is T1, and the temperature of the air T2 after adiabatic
expansion falls below this value (T1
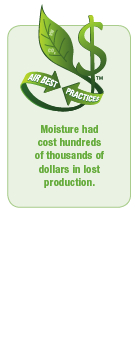
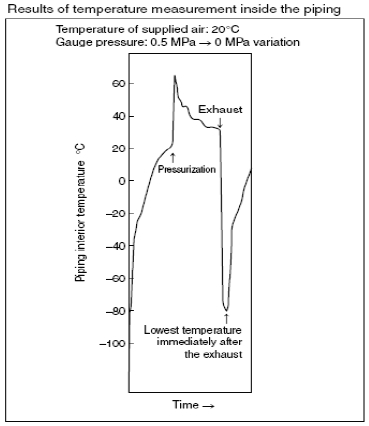
The Solution to Moisture Problems in Pneumatic Cylinders
There is a very effective solution to this
problem, the installation of quick-exhaust valves directly onto the
cylinders. These will allow for the cylinder to fully exhaust on every
cycle, thereby eliminating condensation build up and save the cylinders.
Along with saving the cylinders in the plant, there is no need to keep
the drains of the FRL’s opened in the plant. Leaving the drains opened
is actually creating a larger pressure drop throughout the plant, and
wasting 36 CFM of compressed air.
Understanding what is happening with the
pneumatic cylinders was the key to solving this problem. The facility
had been considering installing desiccant air dryers. This would have
been a significant capital expense and would not have solved the
problem. We were able to identify the adiabatic expansion occurring
between the cylinder and the valve. The solution deployed of
quick-exhaust valve was a minor expense and achieved with little effort.
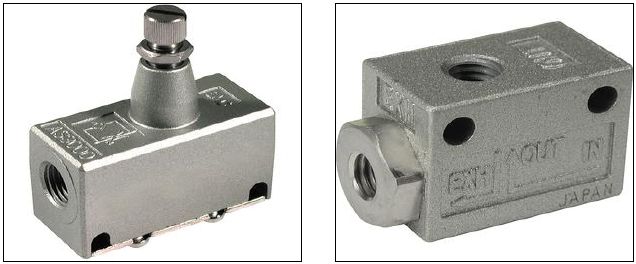
Quick Exhaust Valves Solved the Problems with Moisture
D. Demand Side Audit
Aside from solving the downstream moisture
problem, our audit reviewed pneumatic circuitry in the facility and also
included a compressed air leak audit. Below is a brief summary of some
of the opportunities discovered and solved. The end result was that
air demand was reduced by 186 CFM. This reduced the plant compressed
air demand from an average of 307 CFM to an average of 121 CFM.
The Five Label-Aire Machines
We took note of five Label-Aire machines in
the factory. These units were constantly being pressurized even when
not being used. We conducted a point-of-use test on these machines and
found that each machine consumed an average of 4.2 CFM even when not in
use. We only sampled a fragment of time so we are not sure of what
percentage of the time the machines are idled but plant personnel tell
us that it is a significant percentage of time.
The solution here is to keep the Label-Aire
machines from consuming air when idled. This is easily achieved by the
installation of two-positioned solenoid valves. The
solenoid of these valves will effectively actuate this application only
when the product is present. The solenoid of these two-positioned valves
can be actuated via several applications such as relay sensors and
electronic signals. The table below shows the savings opportunity.
Label-Aire Machines Air Consumption Costs When Idle
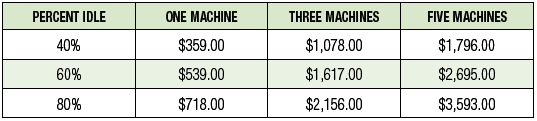
The Ten Blow Guns
There are ten blow guns at the facility
which use inefficient nozzles. This can be costly in the long run due
to the decreased impact pressure and increased waste of compressed air.
We recommend using high-efficiency nozzles, which can reduce air
consumption by 50-75% while increasing the impact pressure at the work
surface. These high-efficiency nozzles utilize the Venturi effect to
gain efficiencies.
High Efficiency Nozzles on Blow Guns
The Cutter Machine Causes Plant Over-pressurization
The cutter machine is causing the entire
plant to run at 100 psig because it requires 95 psig. We conducted a
point-of-use test on this machine to verify its’ air usage. The machine
was operating between 85 and 90 psig when we started the test. Actual
pressure changed over time from 71 psig to 104 psig with 90 being the
average. Air flow went from 20 cfm to 10.4 cfm with 4.3 cfm being the
average. The cutter was actuating twice a minute, in one minute and 15
second cycles with an intermitten down period of approximately two and
one-half minutes.
Due to the intermittent demand of this
application, we are recommending the use of a pneumatic booster coupled
with a air receiver. This will allow us to reduce the air pressure
across the entire facility.
Air Leaks
![]() |
Leak locations in % at the facility |
We have identified and tagged 28 compressed
air leaks in the facility. They account for 120 CFM equating to 39% of
the plants’ average air flow of 307 CFM. Leaks were found on the
airend of one air compressor, and plant-wide on FRL’s, fittings, gauges,
and pneumatic tubing.
It is important to have a leak remediation
campaign in place to keep leaks from consuming unnecessary compressed
air. A proactive approach to leak detection should include all
individuals within the plant and the education of machine operators on
the cost of leaks.
Machine operators could then combat leaks
as they develop by immediately tagging them and notifying maintenance.
This approach to leak remediation is perfect for leaks that can be
easily felt and heard. Some leaks cannot, unfortunately, be detected by
the human ear. We utilize ultrasonic leak detectors to find leaks that
are out of range and hard to hear or feel.
E. Capture the Savings
Air Leak on FRL |
Multiple Holes/Leaks in Tubing |
|
Air Leak on Hose/Fitting Connect |
The demand side audit made it possible for
us to reduce average air demand from 307 CFM to 121 CFM. We fixed leaks
(120 cfm), closed open drain valves (36 cfm), and will reduce over-all
plant pressure (30 cfm). We now need to look at how the compressors are
operating and if they controls are set to capitalize on the new
compressed air demand profile.
The “Before” situation was this to produce 307.3 cfm:
- Compressor #1 ran 100% loaded in modulation mode. At 100% power it had 90 BHP which equated to $74,292 in annual costs of operation.
- Compressor #2 ran 20% loaded in modulation mode. At 78% of power it consumed 67.3 BHP equating to $11,106 in annual energy costs of operation.
- Total annual energy cost of operation was $85,398
The “After” situation was this to produce 121.3 cfm:
- Compressor #1 was placed on standby for emergency situations. $0 energy cost.
- Compressor #2 was capable of having its’ controls modified to Load/No-Load. We ran the machine 37% loaded to meet the demand. At 55% of Power it had 47.45 BHP equating to $39,168 in annual energy costs of operation.
- Total new annual energy cost of operation was $39,168
The new annual energy costs to run the air compressors represents a savings of $46,230 per year.
Conclusion
Understanding pneumatics is core to
conducting a strong demand side audit. Pneumatic circuits were where
the audit was able to discover the dewpoint problem and the
opportunities to reduce air consumption and pressure. Understanding air
compressors and air compressor controls then allowed the installations’
energy costs to be reduced as a result of the demand side improvements.
No comments:
Post a Comment