Program Requirements
The ideal particulate program is comprehensive and able to grow with and into the needs of an organization. Being flexible and versatile allows the program to handle diverse FPM investigations and provides a knowledge bank to query when repeat issues arise. The program should also be cost effective and sustainable, benefitting all levels of staff within the organization. Above all, however, the FPM program should be conclusive, leading to closure for each FPM investigation.Program Components
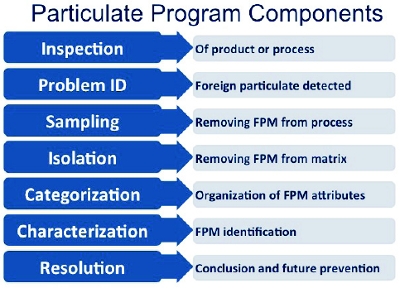
Initial Components
Regulatory requirements necessitate product inspection, and FPM is identified during the initial portions of the program. The next step is removing FPM from the process. Sampling can be as simple as separating finished product containers or as complex as retrieving a residue from the bottom of a 20,000-L tank. Next, the FPM must be isolated from the matrix material. There are numerous techniques for isolation such as pipetting, filtering, or extracting. The most appropriate technique will depend on the specific set of circumstances. Once isolated, FPM should be rinsed with particle-free water to ensure it is free from the matrix material.Isolation requires the most practice and specialized tools because FPM can be as small as 20 μm, which is beyond the visualization limits of the human eye. Therefore, a stereomicroscope must be used to facilitate isolation. Particle sizes range typically from 50-300 μm, but can be as large as a few millimeters (easily seen by the human eye). Using tools, such as a tungsten needle, to manipulate small quantities of material under the stereomicroscope takes practice. Isolation poses a risk to sample integrity through factors like static from the outside environment, by the type of tool that is being used, or by loss if too much pressure is improperly applied with tools. Residual product can also affect the way FPM behaves once it has been exposed to the environment. Less experience with isolation increases risk. It is possible to isolate and evaluate particles smaller than 20 μm, but preparation and characterization strategies are different from those typically used.
Categorization
Categorization allows for flexibility and versatility. During this portion of the program, categories or bins are identified for later use. We categorize many different particle attributes including: morphology (flake, fiber, residue, speck, globular, etc), luster, transparency, color, quantity, mobility, and buoyancy. Additional attributes could be important to particulate found in a manufacturing process, but the relevance of any attribute category will depend on specific processes and circumstances. It is here that optical inspection (or assisted visual inspection) becomes important.Often, specific particle attributes of FPM can only be visualized with the aid of the stereomicroscope. It is possible to have categories from both visual and optical inspection used independently or in concert. Establishing these categories enables trending that assigns value to the FPM data. For example, trending morphology may be of interest. How many fibers have been encountered in production process A? What is the trend in terms of color and a time constraint? How many blue particles were found last year? Is there a particular time of year when one particle type is more prevalent? Categorization is also key in utilizing tiered approaches for cost and efficiency, which are discussed later.
Characterization
Current methods of characterization, such as visual inspection, microscopy, and light obscuration, can support the program up to this point. The main issue is that the information these methods provide, in and of itself, is not adequate enough to trace back to root cause. Figure 2 illustrates an example. All of the particles would appear similar to current methods. The particles are relatively the same size and shape and they have very similar color and luster. However, there are four different sources. Particles A-D are polypropylene, polystyrene, polyethylene terephthalate, and silicone, respectively. Therefore, there are four different root causes to consider. Particulate identification becomes key for root cause determination.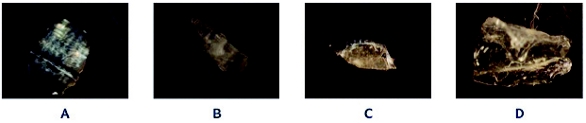
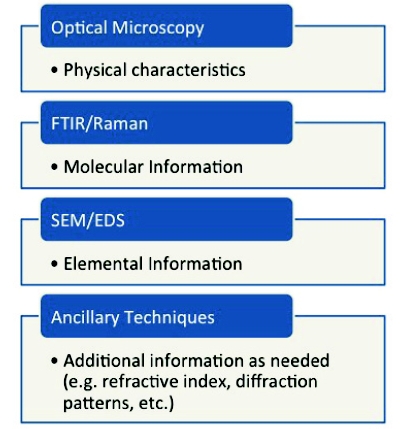
This characterization component allows the program to be comprehensive (clarifies the big picture) and conclusive (leads to root cause) which brings flexibility. A large set of complex data now becomes a living entity that is easily reduced to glean necessary information. Sustainability is also positively impacted because once established, the program can be maintained by individuals with varying technical backgrounds. The tradeoff for this conclusiveness is cost. Quite often, characterization is the most costly component of the program.
Case Studies
These case studies demonstrate the use of FPM program components and include real-world data and scenarios. They lead into a discussion about how tiered approaches can save time and cost in investigations.Case Study 1 – Stability Study Contaminant
FPM was observed during a stability study. It was sampled by sacrificing one of the stability study containers and further isolated by vacuum filtration due to the small size and fragile nature of the particulate. Particulate were categorized as needle-like and were found in high quantity. They were also noted to be clear and crystalline in nature. Characterization identified this material as a polymer additive. After further discussion with the container vendor, it was revealed that the polymer additive matched one that was used to manufacture the containers. It was theorized the high heat of the stability study caused the additive to leach into the product. The issue was resolved by switching to a new container for subsequent studies that could withstand the required temperature. This investigation was lengthy and costly due to the fact that no particulate program was in place. A great deal was understood about the product, but not what could contribute to FPM in the product. Consequently, many potential sources were investigated until the polymer additive was identified by the vendor.Case Study 2 – Finished Product Contaminant
A finished vial of parenteral product contained FPM and was reserved for sampling. The single particle was isolated by direct removal with a stainless steel scalpel blade. Categorization yielded a color and texture like that of the septum material accompanying the vial (gray and malleable). The container closure components of this manufacturing process were well characterized, but there were few other process components included resulting in only a partial program. From characterization, the particle was identified as butyl rubber with silicate fillers which was consistent with the septum material. A review of the process was initiated to identify other potential sources of butyl rubber. After this review, it was concluded that the vial septum was the only potential source of the FPM. An additional forensic technique, fracture matching, was employed to match a gouge in the septum with the shape of the particulate and added to the certainty that this particulate originated from the accompanying septum. A resolution was identified when a study of administration technique showed that personnel puncturing the septum were doing so improperly. Additional training was provided to alleviate the problem. By having a partial program in place, the manufacturer bypassed the need to characterize container closure components for this particular investigation.Case Study 3 – Purification Contaminant
FPM was easily sampled directly from the manufacturing process with simple tools. No further steps were required for isolation. The numerous particles were categorized as white and fibrous. A partial program was also being utilized for this manufacturing process where some process components were fully characterized and some were not. This necessitated the characterization of the FPM which was identified as polypropylene. However, none of the components in the partial program were composed of polypropylene. An investigation was initiated to identify sources of fibrous material outside of those characterized in the program. Eventually, it was revealed the fibrous material was linked to a cleaning component. This component had been substituted and was not fit for the intended purpose. The partial program had been successful in previous investigations in identifying root cause, but failed to facilitate this particular investigation. It did however, cut back on the number of source materials that required investigation.Case Study 4 – Intermediate Production Contaminant
A filter membrane within an intermediate production step contained FPM. The entire filter was sampled and the particulate isolated from the membrane itself. Several particles were categorized as very hard, brittle, and black with a luster. A comprehensive particulate program was established for this manufacturing process and there were several possibilities that fit the categorization attributes (ie, several sources for very hard, brittle, and black particles). The material was characterized as silicon carbide and from this, it was immediately known to source from a gasket seal. Essentially, no additional action was needed and the investigation concluded. This seal was known to wear and the amount of particulate observed was consistent with the wear typically seen at this point of the seal’s lifecycle.From these case studies and in general, the amount of time it takes to conclude an investigation is proportional to the breadth of the particulate program in place (refer to Figure 4 for relative time and costs). That is, Case Study 1 took the most time. Case Studies 2 and 3 were shorter, but could be made more efficient, and Case Study 4 was most efficient due the comprehensive program that was in place. There are some upfront costs associated with program initiation; however, with tiered approaches, comes a possibility to balance these costs against the return of much faster investigation times.
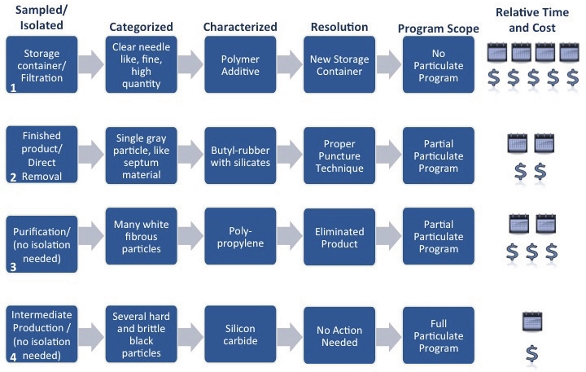
Tiered Approaches
Particulate program requirements include: comprehensiveness, versatility, flexibility, and conclusiveness. These requirements have been satisfied, but the cost effectiveness requirement remains. The flexibility of the program is an advantage for building tiered approaches which can be used to address cost effectiveness.Between the program components of categorization and characterization, there is an opportunity to make decisions about whether or not it is necessary to proceed with characterization. Once pertinent particle attributes have been identified and an established program has historical data to reference, this knowledge base can be combined with a thorough understanding of the manufacturing process. This comprehensive body of knowledge regarding the propensity for FPM can then reduce the need to escalate all particles into the characterization component. This body of knowledge will also help indicate at which manufacturing process steps the particulate profile of the product should be studied and allow boundaries to be set in terms of what to include in the program as a reference materials.
A risk-based approach is then relied upon at the decision point to determine whether the program needs to continue. Risk tolerance of the organization as well as situational risk (eg, healthy versus sick target population, child versus adult population, etc) dictates a forward path. When indications are within risk tolerance, characterization is not necessary. The most cost invasive part of the process is then reserved only for necessary instances. In order to achieve this cost effectiveness, however, the comprehensive program must be built.
Going back to Case Study 2, one could envision a full program showing that no butyl rubber sources aside from the septum existed in the process. It would also be known through establishment and routine use of the program that each time a gray, malleable particle is seen, there is confidence the material is butyl rubber. This collective information is used to eliminate the need to characterize the FPM. Each time a gray, malleable particle is encountered, it is within the risk tolerance to assume consistency with the septum material.
Case Study 4 provides an additional example. One could envision in this case the instance where no other particles matched the categorization attributes of the encountered FPM. The investigation would essentially be concluded at categorization. Time and costs are eliminated from the process. The most costly part of the program is used only when necessary and reserved for situations like anomaly particles or particles with similar categorization attributes.
FPM in the Lifecycle
The program and its components have been discussed thus far. How is this program proactive versus reactive and how does it fit into the product lifecycle? Traditionally, FPM investigations are linked to latter portions of the product lifecycle. Something is encountered in manufacturing and reacted to by initiating an investigation. To be more proactive, forethought should extend into earlier portions of the lifecycle even as far as clinical trials. This creates the mindset to consider particulate before it becomes a problem.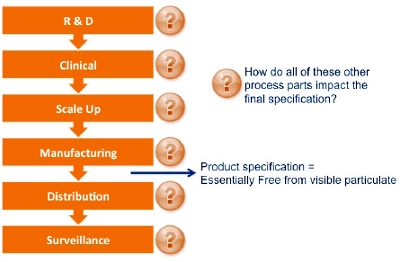
This task can sound overwhelming and daunting; however, the natural segments of the process can be used to delineate how to begin addressing it. A certain level of process understanding will exist and is then built upon through the natural lifecycle. This is the approach to addressing FPM that is very much in line with QbD.
No comments:
Post a Comment