In American English, the term furnace on its own is generally used to describe household heating systems based on a central furnace (known either as a boiler or a heater in British English), and sometimes as a synonym for kiln, a device used to fire clay to produce ceramics. In British English the term furnace is used exclusively to mean industrial furnaces which are used for many things, such as the extraction of metal from ore (smelting) or in oil refineries and other chemical plants, for example as the heat source for fractional distillation columns.
The term furnace can also refer to a direct fired heater, used in boiler applications in chemical industries or for providing heat to chemical reactions for processes like cracking, and is part of the standard English names for many metallurgical furnaces worldwide.
Unique furnaces are used to run fire tests to qualify fire protection products for use in construction.
The heat energy to fuel a furnace may be supplied directly by combustion of some fuel, or electric furnaces such as the electric arc furnace or induction furnace use remotely generated electric power.
Household Furnaces
A household furnace is a major appliance that is permanently installed to provide heat to an interior space through intermediary fluid movement, which may be air, steam, or hot water. The most common fuel source for modern furnaces in the United States is natural gas; other common fuel sources include LPG (liquefied petroleum gas), fuel oil, coal or wood. In some cases electrical resistance heating is used as the source of heat, especially where the cost of electricity is low.Combustion furnaces always need to be vented to the outside. Traditionally, this was through a chimney, which tends to expel heat along with the exhaust. Modern high-efficiency furnaces can be 98% efficient and operate without a chimney. The small amount of waste gas and heat are mechanically ventillated through a small tube through the side or roof of the house.
- "High-efficiency" in this sense may be misleading, because furnace efficiency is typically expressed as a "first-law" efficiency, whereas the exergy efficiency of a typical furnace is much lower than the first-law thermal efficiency. By comparison, cogeneration has a higher exergy efficiency than is realizable from burning fuel to generate heat directly at a moderate temperature. However, as the vast majority of consumers (as well as many government regulators) are unfamiliar with exergy efficiency, Carnot efficiency, and the Second Law of Thermodynamics, the use of first-law efficiencies to rate furnaces is well-entrenched.
Heat Distribution
The furnace transfers heat to the living space of the building through an intermediary distribution system. If the distribution is through hot water (or other fluid) or through steam, then the furnace is more commonly termed a boiler. One advantage of a boiler is that the furnace can provide hot water for bathing and washing dishes, rather than requiring a separate water heater.

A condensing furnace.
Air convection heating systems have been in use for over a century, but the older systems relied on a passive air circulation system where the greater density of cooler air caused it to sink into the furnace, and the lesser density of the warmed air caused it to rise in the ductwork, the two forces acting together to drive air circulation in a system termed "gravity-feed; the layout of the ducts and furnace was optimized for short, large ducts and caused the furnace to be referred to as an "octopus" furnace.
By comparison, most modern "warm air" furnaces typically use a fan to circulate air to the rooms of house and pull cooler air back to the furnace for reheating; this is called forced-air heat. Because the fan easily overcomes the resistance of the ductwork, the arrangement of ducts can be far more flexible than the octopus of old. In American practice, separate ducts collect cool air to be returned to the furnace. At the furnace, cool air passes into the furnace, usually through an air filter, through the blower, then through the heat exchanger of the furnace, whence it is blown throughout the building. One major advantage of this type of system is that it also enables easy installation of central air conditioning by simply adding a cooling coil at the exhaust of the furnace.
Air is circulated through ductwork, which may be made of sheet metal or plastic "flex" duct and insulated or uninsulated. Unless the ducts and plenums have been sealed using mastic or foil duct tape, the ductwork is likely to have a high leakage of conditioned air, possibly into unconditioned spaces. Another cause of wasted energy is the installation of ductwork in unheated areas, such as attics and crawl spaces; or ductwork of air conditioning systems in attics in warm climates.
The following rare but difficult-to-diagnose failure can occur. If the temperature inside the furnace exceeds a maximum threshold, a safety mechanism with a thermostat will shut the furnace down. A symptom of this failure is that the furnace repeatedly shuts down before the house reaches the desired temperature; this is commonly referred to as the furnace "riding the high limit switch". This condition commonly occurs if the temperature setting of the high limit thermostat is set too close to the normal operating temperature of the furnace. Another situation may occur if a humidifier is incorrectly installed on the furnace and the duct which directs a portion of the humidified air back into the furnace is too large. The solution is to reduce the diameter of the cross-feed tube, or install a baffle that reduces the volume of re-fed air.
Metallurgical furnaces
In metallurgy, several specialised furnaces are used. These include:- Furnaces used in smelters, including:
- The blast furnace, used to reduce iron ore to pig iron
- Steelmaking furnaces, including:
- Puddling furnace
- Reverberatory furnace
- Bessemer converter
- Open hearth furnace
- Basic oxygen furnace
- Electric arc furnace
- Electric induction furnace
- Furnaces used to remelt metal in foundries.
- Furnaces used to reheat and heat treat metal for use in:
- Rolling mills, including tinplate works and slitting mills.
- Forges.
- Vacuum furnaces
See also
- Extractive metallurgy
- Flue gas stacks
- Reverberatory furnace
- Fire test
Industrial furnaces
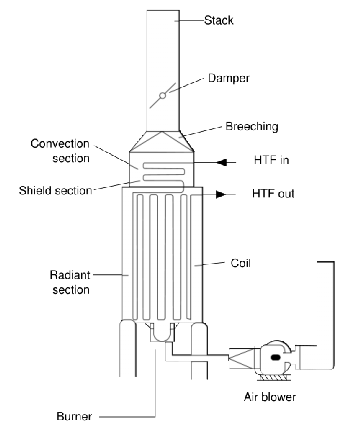
Fuel flows into the burner and is burnt with air provided from an air blower. There can be more than one burner in a particular furnace which can be arranged in cells which heat a particular set of tubes. Burners can also be floor mounted as in the picture, wall mounted or roof mounted depending on design. The flames heat up the tubes, which in turn heat the fluid inside in the first part of the furnace known as the radiant section. In the chamber where combustion takes place, known as the firebox, the heat is transferred mainly by radiation to tubes around the fire in the chamber. The heating fluid passes through the tubes and is thus heated to the desired temperature. The gases from the combustion are known as flue gas. After the flue gas leaves the firebox, most furnace designs include a convection section where more heat is recovered before venting to the atmosphere through the flue gas stack. (HTF=Heat Transfer Fluid. Industries commonly use their furnaces to heat a secondary fluid with special additives like anti-rust and high heat transfer efficiency. This heated fluid is then circulated round the whole plant to heat exchangers to be used wherever heat is needed instead of directly heating the product line as the product or material may be volatile or prone to cracking at the furnace temperature.)
Radiant section
The radiant section is where the tubes receive almost all its heat by radiation from the flame. In a vertical, cylindrical furnace, the tubes are vertical. Tubes can be vertical or horizontal, placed along the refractory wall, in the middle, etc., or arranged in cells. Studs are used to hold the insulation together and on the wall of the furnace. They are placed about 1 ft (300 mm) apart in this picture of the inside of a furnace. The tubes, which are reddish brown from corrosion, are carbon steel tubes and run the height of the radiant section. The tubes are a distance away from the insulation so radiation can be reflected to the back of the tubes to maintain a uniform tube wall temperature. Tube guides at the top, middle and bottom hold the tubes in place.Convection section
The convection section is located above the radiant section where it is cooler to recover additional heat. Heat transfer takes place by convection here, and the tubes are finned to increase heat transfer. The first two tube rows in the bottom of the convection section and at the top of the radiant section is an area of bare tubes (without fins) and are known as the shield section, so named because they are still exposed to plenty of radiation from the firebox and they also act to shield the convection section tubes, which are normally of less resistant material from the high temperatures in the firebox. The area of the radiant section just before flue gas enters the shield section and into the convection section called the bridgezone. Crossover is the term used to describe the tube that connects from the convection section outlet to the radiant section inlet. The crossover piping is normally located outside so that the temperature can be monitored and the efficiency of the convection section can be calculated. The sightglass at the top allows personnel to see the flame shape and pattern from above and visually inspect if flame impingement is occurring. Flame impingement happens when the flame touches the tubes and causes small isolated spots of very high temperature.Burner
The burner in the vertical, cylindrical furnace as above, is located in the floor and fires upward. Some furnaces have side fired burners, eg: train locomotive. The burner tile is made of high temperature refractory and is where the flame is contained in. Air registers located below the burner and at the outlet of the air blower are devices with movable flaps or vanes that control the shape and pattern of the flame, whether it spreads out or even swirls around. Flames should not spread out too much, as this will cause flame impingement. Air registers can be classified as primary, secondary and if applicable, tertiary, depending on when their air is introduced. The primary air register supplies primary air, which is the first to be introduced in the burner. Secondary air is added to supplement primary air. Burners may include a premixer to mix the air and fuel for better combustion before introducing into the burner. Some burners even use steam as premix to preheat the air and create better mixing of the fuel and heated air. The floor of the furnace is mostly made of a different material from that of the wall, eg: hard castable refractory known as kastolite so the floor can be walked on during maintenance.A furnace can be lit by a small pilot flame or in some older models, matches... Most pilot flame nowadays are lit by an ignition transformer (much like a car's spark plugs). The pilot flame in turn lights up the main flame. The pilot flame uses natural gas while the main flame can use both diesel and natural gas. When using liquid fuels, an atomizer is used, otherwise, the liquid fuel will simply pour onto the furnace floor and become a hazard. Using a pilot flame for lighting the furnace increases safety and ease. (compared to using a match)
Sootblower
Sootblowers are found in the convection section. As this section is above the radiant section and air movement is slower because of the fins, soot tends to accumulate here. Sootblowing is normally done when the efficiency of the convection section is decreased. This can be calculated by looking at the temperature change from the crossover piping and at the convection section exit. Sootblowers utilize flowing media such as water, air or steam to remove deposits from the tubes. There are several different types of sootblowers used. Wall blowers are used for furnace walls and have a very short lance with a nozzle at the tip. The lance has holes drilled into it at intervals so that when it is turned on, it rotates and cleans the deposits from the wall in a circular pattern. After it has turned a predetermined number of rounds, the sootblowing is completed and stops.Stack
The flue gas stack is a cylindrical structure at the top of all the heat transfer chambers. The breeching directly below it collects the flue gas and brings it up high into the atmosphere where it will not endanger personnel.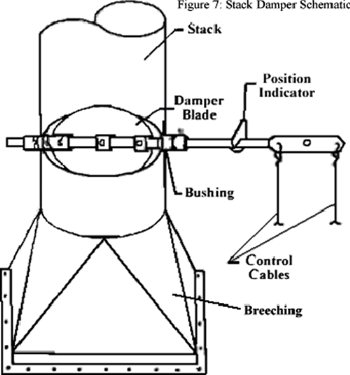
Insulation
Insulation is an important part of the furnace because it prevents excessive heat loss. Refractory materials such as firebrick, castable refractories and ceramic fibre, are used for insulation. The floor of the furnace is normally castable since it has to be hard enough to walk on during maintenance. Ceramic fibre is commonly used for the roof and wall of the furnace and is graded by its density and then its maximum temperature rating. For eg: 8# 2,300°F means 8 lb/ft3 density with a maximum temperature rating of 2,300°F. An example of a castable is kastolite.Outdoor Wood-Fired Boilers
Description
An outdoor wood-fired boiler (OWB) also known as a waterstove or outdoor wood furnace, is a heating technology that has grown in popularity in the Northern United States. OWBs in most cases look like a small shack with metal siding. They are self-contained, and are only connected to the building they heat through underground insulated water pipes. OWBs contain a metal combustion chamber for a wood fire, which is surrounded by a water tank or water jacket. The fire heats the water, which is then circulated through the insulated water pipes into the heated building. Once the hot water from the boiler reaches the building, the heat from the hot water can be transferred to most existing heating systems and the building's hot water supply.A damper and fan on the boiler interact with a thermostat inside the building. If the building's temperature falls, the thermostat will trigger the damper to open, letting oxygen enter the combustion chamber, which causes the fire to burn more intensely. The fire will then raise the temperature of the water which increases the heat supplied to the home.
Benefits
OWBs have several benefits that increase their popularity. Their large combustion chamber accommodates more fuel than many other forms of wood heat, decreasing the number of times an owner has to add fuel to the fire. Home insurance may cost more for people who heat with an indoor form of wood heat than with an OWB [1]. Finally, for people with a large supply of free wood and willing to invest the time to prepare the wood and stock the OWB, an OWB can be less expensive than heating with gas, oil, or electricity.Controversy
OWBs are not without controversy, as their emissions sometimes bother neighbors. Some states and municipalities have banned the devices[2]. They are not currently regulated by the United States Environmental Protection Agency (EPA), unlike other forms of wood heat [3]. (However, recently the EPA has worked with manufacturers to develop a method for manufacturers to identify OWBs that meet a voluntary emissions standard [4].) Studies conducted on OWBs suggest that these devices may produce more emissions, most notably particulate matter under 2.5 micrometres (PM2.5) than other heating technologies, though manufacturers dispute these assessments [5]. Exposure to elevated levels of PM2.5 has been associated with cardiopulmonary health effects and premature death [6]As of July 2006, the HPBA, along with many of the major OWB manufactures, have requested users of their products follow the "Outdoor Wood Furnace Best Burn Practices" [7] These guidelines have been set up by the HPBA to help cut down on problems associated with OWBs.
References
- Gray, W.A. and Muller, R (1974). ''Engineering calculations in radiative heat transfer, 1st Edition, Pergamon Press Ltd. ISBN 0-08-017786-7 or ISBN 0-08-017787-5.
- Fiveland, W.A., Crosbie, A.L., Smith A.M. and Smith, T.F. (Editors) (1991). Fundamentals of radiation heat transfer. American Society of Mechanical Engineers. ISBN 0-7918-0729-0.
- Warring, R. H (1982). Handbook of valves, piping and pipelines, 1st Edition, Gulf Publishing Company. ISBN 0-87201-885-7.
- Dukelow, Samuel G (1985). Improving boiler efficiency, 2nd Edition, Instrument Society of America. ISBN 0-87664-852-9.
- Whitehouse, R.C. (Editor) (1993). The valve and actuator user's manual. Mechanical Engineering Publications. ISBN 0-85298-805-2.
- Davies, Clive (1970). Calculations in furnace technology, 1st Edition, Pergamon Press. ISBN 0080133665.
- Goldstick, R. and Thumann, A (1986). Principles of waste heat recovery. Fairmont Press. ISBN 0-88173-015-7.
- ASHRAE (1992). ASHRAE Handbook. Heating, ventilating and air-conditioning systems and equipment. ASHRAE. ISSN 1078-6066.
- Perry, R.H. and Green, D.W. (Editors) (1997). Perry's Chemical Engineers' Handbook, 7th Edition, McGraw-Hill. ISBN 0-07-049841-5.
- Lieberman, P. and Lieberman, Elizabeth T (2003). Working Guide to Process Equipment, 2nd Edition, McGraw-Hill. ISBN 0-07-139087-1.
- Screamo Band from New Hampshire
9 comments:
Sometimes it can be hard to choose a good heating repair service that both correct the heating repair issue quickly and at a reasonable cost.
Furnace service Toronto
Furnace for thermal application is indispensable; it reduces the cost of manufacturing in metal applications.
Baxi Ecogen looks and acts just like a conventional boiler and the basic principles for heating are the same as a regular boiler.
Boiler heating treatment in Ontario Canada
Thanks for sharing these HVAC blog sites. I will get benefit from it in the future.
www.cosmopolitanmechanical.ca
تساهم شركات طلمبات ومضخات الحريق في حفظ الأمن والسلامة في مصر. فعند وقوع حريق، يعتمد استجابة سريعة وفعالة على توفر أنظمة إطفاء الحريق المناسبة والتي تعتمد بشكل أساسي على الطلمبات والمضخات. تلعب هذه الأنظمة دورًا حاسمًا في السيطرة على الحرائق والحد من الأضرار المحتملة، وبالتالي تساهم في حفظ الأرواح والممتلكات.
تركيب شيش حصيرة تركي الألوميتال يعتبر من الأمور المهمة في عملية تركيب الواجهات الزجاجية والأبواب والنوافذ، حيث يعمل على تثبيت الزجاج بشكل آمن وفعال
انسداد الشريان السباتي هو حالة تحدث عندما يتم انسداد الشريان الذي يمر في منطقة الأذن والجبهة. وهو يحدث بسبب تراكم الدهون أو التصاق التخثرات داخل الشريان ومن أجل علاج ضيق الشريان السباتي لابد من التعامل مع طبيب مختص وذو خبرة
يذكر الدكتور محمود ناصر افضل دكتور متخصص في علاج الدوالي بدون جراحة بتقنية الكلاكس في مصر ان أعراض انسداد الشريان السباتي متنوعة وتشمل:
- آلام في المنطقة المصابة.
- صعوبة في فتح الفم.
- صعوبة في التحدث.
Post a Comment